PROFIBUS DP Slave Hardware
The FieldServer PROFIBUS DP Slave gateway makes it easy for integrators to interface devices utilizing various building or industrial protocols to PROFIBUS DP Slave networks. As the leading manufacturer of protocol gateways in the building automation industry, FieldServer has developed the largest driver library in the industry and the widest range of gateways available, designed to meet the needs of system integrators.
The FS-B3512-05 provides a wealth of features to enable data transfer between different devices and networks utilizing serial (RS-232 or RS-485), Ethernet, LonWorks and PROFIBUS DP Master. The multiport design allows for serial-to-serial, serial-to-Ethernet, LonWorks and PROFIBUS DP Slave interfaces. With a larger point count than any similar gateway, the FieldServer FS-B35 series provides a single device solution for your networking needs. The FieldServer is designed to meet a wide range of interface needs and it is easily configured as a master or a slave.
Configuration is easy, but if needed, configuration services are available from FieldServer support team. The proven FieldServer support team is recognized around the world for its knowledge of the many different protocols involved in building automation.
FieldServer continuously strives to enhance our gateways and the latest FS-B35 series includes a major software upgrade, resulting in significant enhancements in performance, including:
- 40% higher point count capability - some protocols are major memory hogs, and the result is that they can slow down performance of any gateway. With the greater memory enhancement, the FS-B35 Series can easily handle all of the drivers extremely well.
- Memory utilization monitoring - the user is provided with application memory statistics (in both kB and as a percentage of the available memory) enabling optimal matching of device models and configurations to specific applications.
- Improved stability and performance under high loads - the new software enhances the operation making it more forgiving to configuration problems with fewer crashes when capacity limits are reached.
- USB firmware update - this allows the firmware or configuration of the FieldServer to be updated from a USB flash drive whenever it is inserted, enabling users to easily update firmware in the field. This is a great time saver if you have multiple FieldServers in the field.
DNP3.0 Ethernet
The Ethernet DNP 3.0 driver allows the FieldServer to transfer data to and from devices over Ethernet using DNP 3.0 protocol. The FieldServer can emulate either a Server of Client. The DNP 3.0 Ethernet Driver adheres to and supports the framework specified by the IEEE 1815-2012 Standard for electrical power system communications.
The following information was copied form the DNP 3.0 User Group Internet site.
The development of DNP3 was a comprehensive effort to achieve open, standardsbased Interoperability between substation computers, RTUs, IEDs (Intelligent Electronic Devices) and master stations (except inter-master station communications) for the electric utility industry. Also important was the time frame; the need for a solution to meet today's requirements. As ambitious an undertaking as this was, we reached this objective. And since the inception of DNP, the protocol has also become widely utilized in adjacent industries such as water / waste water, transportation and the oil and gas industry.
DNP3 is based on the standards of the International Electrotechnical Commission (IEC) Technical Committee 57, Working Group 03 who have been working on an OSI 3 layer "Enhanced Performance Architecture" (EPA) protocol standard for telecontrol applications. DNP3 has been designed to be as close to compliant as possible to the standards as they existed at time of development with the addition of functionality not identified in Europe but needed for current and future North American applications (e.g. limited transport layer functions to support 2K block transfers for IEDs, RF and fiber support). DNP3 has been selected as a Recommended Practice by the IEEE C.2 Task Force; RTU to IED Communications Protocol.
DNP3 is an open and public protocol. In order to ensure interoperability, longevity and upgradeability of, protocol the DNP3 Users Group has taken ownership of the protocol and assumes responsibility for its evolution. The DNP3 Users Group Technical Committee evaluates suggested modifications or additions to the protocol and then amends the protocol description as directed by the Users Group members.
DNP3 Features: DNP3 offers flexibility and functionality that go far beyond conventional communications protocols. Among its robust and flexible features DNP3 includes:
- Output options
- Secure configuration/file transfers
- Addressing for over 65,000 devices on a single link
- Time synchronization and time-stamped events
- Broadcast messages
- Data link and application layer confirmation
DNP3 was originally designed based on three layers of the OSI seven-layer model: application layer, data link layer and physical layer. The application layer is objectbased with objects provided for most generic data formats. The data link layer provides for several methods of retrieving data such as polling for classes and object variations. The physical layer defines most commonly a simple RS-232 or RS-485 interface.
DNP3 is very efficient for a layered protocol while ensuring high data integrity
DNP3 Benefits: Because DNP3 is based on the IEC 870-5 requirements, DNP3 is suitable for application in the entire SCADA environment. This includes RTU to IED communications, master to remote communications, and even peer-to-peer instances and network applications.
Being an object-based application layer protocol, DNP3 has the flexibility to support multiple operating modes such as poll-response, polled report-by-exception, unsolicited responses and peer-to-peer. It permits multiple masters and encourages distributed intelligence.
Users can expect many benefits from using DNP3. In the short term:
- Interoperability between multi-vendor devices
- Fewer protocols to support in the field
- Reduced software costs
- No protocol translators needed
- Shorter delivery schedules
- Less testing, maintenance and training
- Improved documentation
- Independent conformance testing
- Support by independent users group and third-party sources (e.g. test sets, source code)
Profibus DP Slave
The FieldServer Profibus DP Slave driver can be
used to emulate a single slave station on a Profibus
network. DP Masters can open a connection of up to
244 Bytes of Input and 244 Bytes of Output data, but
not exceeding a combined total of 416 Bytes to the
FieldServer. The FieldServer can be added to the
Profibus network with the use of the supplied GSD
file for the ANYBUS card. Connection to the
Profibus network is via a DB9 port on the ANYBUS
card.
Specifications
Field Connections
- Ethernet Ports – 2: 100 BaseT RJ45 connector (auto MDIX and sensing) with ESD protection
- Serial Ports – 5: 2 x RJ45 RS-232 galvanically isolated with ESD protection. 2 x RS-485 galvanically isolated with ESD protection. 1 x RJ45 RS-232 system port.
- Profibus DP - 1: PROFIBUS DP Slave. Standard PROFIBUS connector. Auto baudrate. Can emulate one PROFIBUS DP Slave Station (244 Bytes Input 244 Bytes Output Other Combined 416 Bytes)
- LonWorks – 1: FTT-10 twisted pair. 1000 Network variable capability. LonWorks service pin
- Auxiliary ports – 2: 2 x USB ports. Expansion: Fieldbus connectors available for selected protocol
Environment
- Operating Temperature: 0-60 °C (32-140 °F)
- Relative Humidity: 10-90% non-condensing
Power Requirements
24V AC (+/-10%) or 12-30V DC @ 12W
Physical Dimensions
- Dimensions (WxDxH): 6.3x5.4x2.0 in.(16.0x13.7x5.0cm)
- Weight: 2.5 lbs (1.5 Kg)
- Input voltage: 24 V DC nominal: 10-30V DC
Other
Configuration/Diagnostic utilities
- Capacity: Base system has 1000 point capability (upgradeable to 10,000 points)
- Mounting Options: Desktop, Wall, Panel Optional: DIN rail
LED Indicators
Power, Run, System Error, Configuration Error, and Node Offline
Ethernet connection– Link OK, Tx/Rx communication activity
RS-232/RS-485 – Tx/Rx communication activity
LonWorks - Activity
Communication, Option, Drivers
Memory upgrade for additional data points
Custom Configuration Service
Drivers available for a wide range of Ethernet and social protocols
Approvals
- CE Marked
- CSA Certified: UL916 Standard and CSA @ 22.2
- DNP 3.0 Tested
- RoHS Compliant
- GOST-R Certified
- FCC: Part 15
- LonMark Certified
- Modbus Tested
- BTL Certified
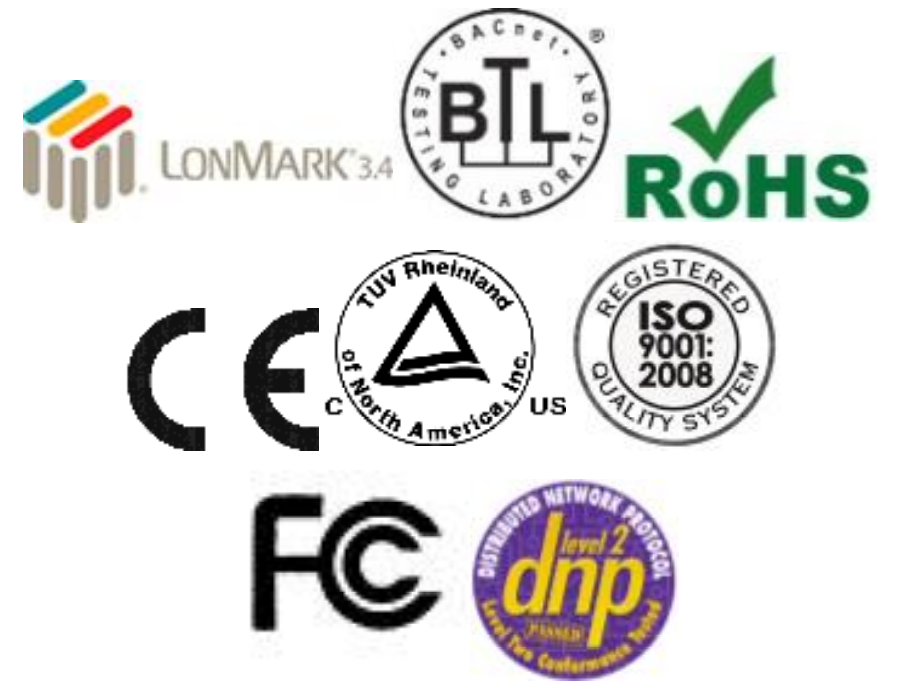