DNP 3.0 Ethernet/Serial Gateways, Services, and Resources
Intro to DNP 3.0
DNP3 (Distributed Network Protocol) is a set of communications protocols used between components in process automation systems. Its main use is in utilities such as electric and water companies. DNP3 was developed for communications between various types of data acquisition and control equipment and plays a crucial role in SCADA systems, where it is used by SCADA Master Stations (a.k.a. Control Centers), Remote Terminal Units (RTUs), and Intelligent Electronic Devices (IEDs).
DNP3 is primarily used for communications between a master station and RTUs or IEDs and pronunciation occurs via serial or ethernet. Competing standards include the older Modbus protocol and the newer IEC 61850 protocol.
QuickServer for DNP 3.0
The DNP3 QuickServer (QS) is a high-performance, fully configurable, and cost-effective protocol gateway for integrating any DNP3 System. The Gateway comes basic (250 points) and enhanced (500 points) and can connect to serial (RS485 and RS232) and Ethernet ports. DNP3 comes in Ethernet and Serial versions. Chipkin knows this protocol to source code level – get expert support (Level 1,2) and configuration from day 1.
We carry a wide selection of DNP3 gateways that can connect to over 150+ protocols. If you're interested in a DNP3 Gateway, view our selection. Or, please Contact Us for a free consultation or quote.
Dual-Ethernet Port QuickServer for DNP 3.0
The Dual Ethernet Port QuickServer is the premium secure QuickServer for those needing the best and most secure networks. Besides being capable of handling everything that the classic QuickServer and the QuickServer can handle, it also contains 2 Ethernet ports, can convert up to 10,000 points and has a lot of new security features. It supports 1 RS-485/RS232 Port, 1 RS485 Port, and two Ethernet ports.
With two Ethernet ports, the dual-port QuickServer allows data to move seamlessly across disparate subnets allowing seamless integration with maximum security.
Multiport Gateway for DNP 3.0
The FS-B3510 is one of the FS-X30 Series FieldServers designed to meet the needs of any system integrator. The FS-B30 Series brings together the powerful FieldServer driver library with state-of-the-art gateway design. It supports 1,000 points which can be updrageded to 10,000 points allowing it to easily handle just about anything with no slowdown in performance.
Chipkin provides DNP 3.0 gateways for a wide number of conversions. Please Contact Us for a free consultation.
DNP3 Block Diagram
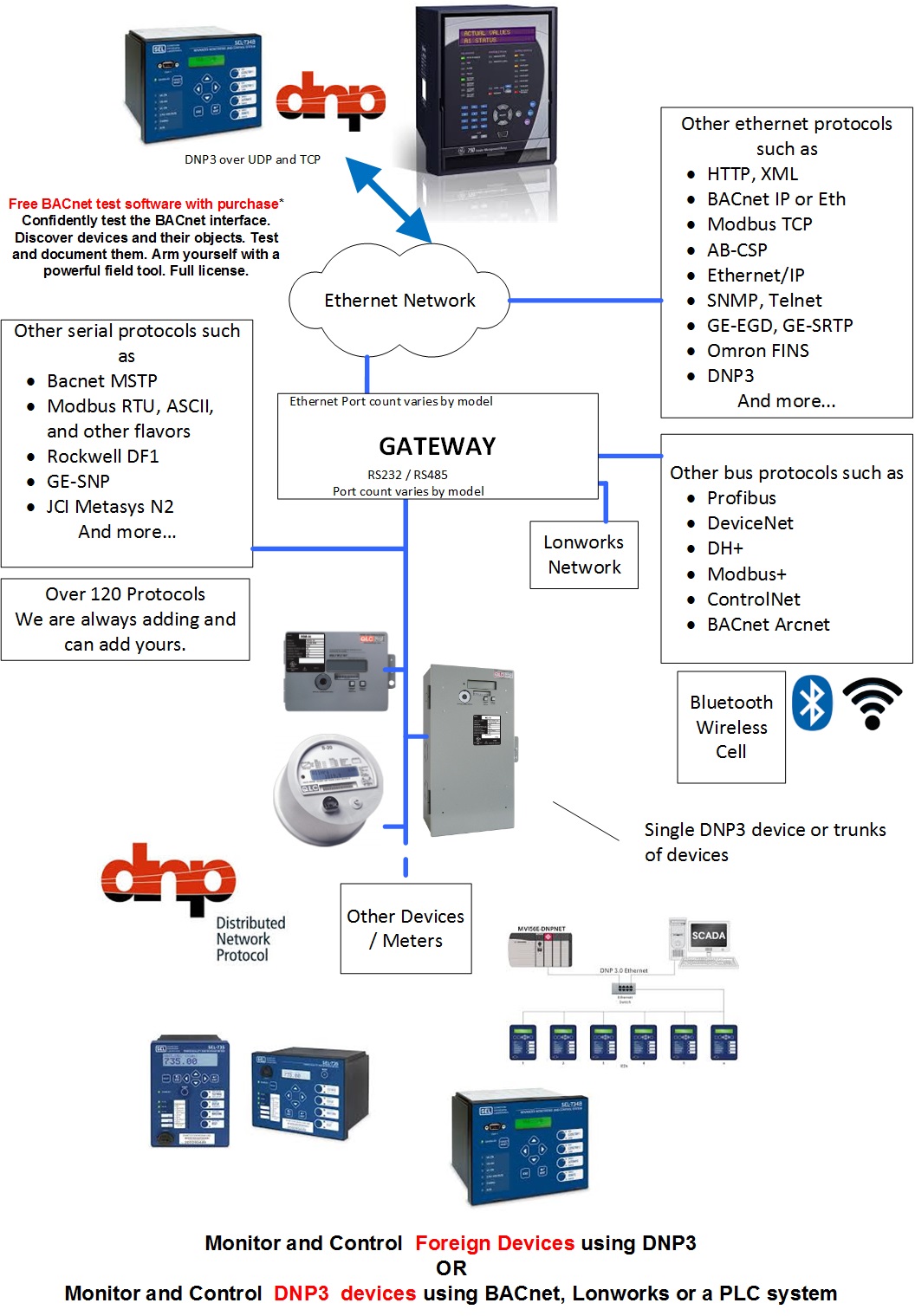
DNP3 Datasheets, Manuals and other resources
DNP 3.0 has a large number of products and applications. See below for a bit of Knowledge:
DNP 3.0 Gateways (Protocol Converters)
DNP 3.0 Serial and Ethernet
- DNP 3.0 Serial to Modbus RTU
- DNP 3.0 Ethernet to Modbus RTU
- DNP 3.0 Ethernet to Veeder Root
- DNP 3.0 Serial to DNP 3.0 Ethernet
- DNP 3.0 Serial to GE-SRTP
- DNP 3.0 Serial to SNMP
- DNP 3.0 Serial to BACnet IP
- DNP 3.0 Serial to Modbus TCP
- DNP 3.0 Serial to Ethernet IP
- DNP 3.0 Serial to BACnet MSTP
- DNP 3.0 Serial to Metasys N2
- DNP 3.0 Ethernet to SNMP
- DNP 3.0 Ethernet to Modbus TCP
- DNP 3.0 Ethernet to ControlLogix for SlotServer
- DNP 3.0 Serial to LonWorks
- DNP 3.0 Ethernet to LonWorks
- DNP 3.0 Ethernet to Ethernet IP
- DNP 3.0 Ethernet to DNP 3.0 Serial
- DNP 3.0 Ethernet to BACnet Ethernet
- DNP 3.0 Ethernet to Profibus DP Slave
- DNP 3.0 Serial to Profibus DP Slave
- DNP 3.0 Ethernet to BACnet IP
- DNP 3.0 Ethernet to BACnet MSTP
- DNP 3.0 Ethernet to General Purpose ASCII
- DNP 3.0 Ethernet to Ethernet IP
- DNP 3.0 Ethernet to AB CSP
- DF1 to DNP 3.0 Serial or DNP 3.0 Ethernet
- DNP 3.0 Serial or DNP 3.0 Ethernet to Lutron Grafik 6000
- DNP 3.0 Serial or DNP 3.0 Ethernet to Carrier DataLink
- McQuay to DNP 3.0 Serial or DNP 3.0 Ethernet
- DNP 3.0 Serial or DNP 3.0 Ethernet to Notifier INA
- Caterpillar M5X to DNP 3.0 Serial or DNP 3.0 Ethernet
- Notifier Onyx 640 to DNP 3.0 Serial or DNP 3.0 Ethernet
- DNP 3.0 Serial or DNP 3.0 Ethernet to Data Aire DAP
- DNP 3.0 Serial or DNP 3.0 Ethernet to Data Aire DART
- Secutron to DNP 3.0 Serial or DNP 3.0 Ethernet
- DNP 3.0 Serial or DNP 3.0 Ethernet to TAC INet 2000
- DNP 3.0 Serial or DNP 3.0 Ethernet to RussElectric Model 2000
- DNP 3.0 Serial or DNP 3.0 Ethernet to Silent Knight
- DNP 3.0 Serial or DNP 3.0 Ethernet to ATMI ACM
- AB CSP to DNP 3.0 Serial or DNP 3.0 Ethernet
- Notifier Italia AM6000 to DNP 3.0 Serial or DNP 3.0 Ethernet
- XML to DNP 3.0 Serial or DNP 3.0 Ethernet
- Fike Cheetah to DNP 3.0 Serial or DNP 3.0 Ethernet
- XML to DNP 3.0 Serial or DNP 3.0 Ethernet
- Notifier Onyx 640 to DNP 3.0 Serial or DNP 3.0 Ethernet
- DNP 3.0 Serial or DNP 3.0 Ethernet to Notifier NCA
- DNP 3.0 Serial or DNP 3.0 Ethernet to AB CSP
- DNP 3.0 Serial or DNP 3.0 Ethernet to Bacnet Ethernet
- DNP 3.0 Serial or DNP 3.0 Ethernet to Lutron Machine
- DNP 3.0 Serial or DNP 3.0 Ethernet to Notifier 3030
- DNP 3.0 Serial or DNP 3.0 Ethernet to GE-SNP
- DNP 3.0 Serial or DNP 3.0 Ethernet to Mudbus Jbus
- DNP 3.0 Serial or DNP 3.0 Ethernet to Gardner Denver
- DNP 3.0 Serial or DNP 3.0 Ethernet to Grinnell TFX Minerva
- DNP 3.0 Serial or DNP 3.0 Ethernet to Simplex 4100
- DNP 3.0 Serial or DNP 3.0 Ethernet to EST3 Serial
- DNP 3.0 Serial or DNP 3.0 Ethernet to Modbus Tek-Air
- DNP 3.0 Serial or DNP 3.0 Ethernet to Cleaver Brooks Hawk
- BACnet PTP Serial to DNP 3.0 Serial or DNP 3.0 Ethernet
- Hochiki Serial Driver to DNP 3.0 Serial or DNP 3.0 Ethernet
- Notifier 1010/2020 to DNP 3.0 Serial or DNP 3.0 Ethernet
- Canatal to DNP 3.0 Serial or DNP 3.0 Ethernet
- Zellweger Infratox to DNP 3.0 Serial or DNP 3.0 Ethernet
- DNP 3.0 Serial or DNP 3.0 Ethernet to Notifier 200/300/400
Description of the DNP 3.0 Serial Driver
The DNP3 Serial driver allows the FieldServer to transfer data to and from devices over RS-232 or RS485 using DNP3 protocol. The FieldServer can emulate either a Server or Client. When the FieldServer is a Server (slave), only one Client (master) can communicate to it. The DNP3 Serial Driver adheres to and supports the framework specified by the IEEE 1815-2012 Standard for electrical power system communications.
The following information was copied from the DNP3 User Group Internet site
The development of DNP3 was a comprehensive effort to achieve open, standards-based Interoperability between substation computers, RTUs, IEDs (Intelligent Electronic Devices) and master stations (except inter-master station communications) for the electric utility industry. Also important was the time frame; the need for a solution to meet today's requirements. As ambitious an undertaking as this was, we reached this objective. And since the inception of DNP, the protocol has also become widely utilized in adjacent industries such as water / waste water, transportation and the oil and gas industry.
DNP3 is based on the standards of the International Electrotechnical Commission (IEC) Technical Committee 57, Working Group 03 who have been working on an OSI 3 layer "Enhanced Performance Architecture" (EPA) protocol standard for telecontrol applications. DNP3 has been designed to be as close to compliant as possible to the standards as they existed at time of development with the addition of functionality not identified in Europe but needed for current and future North American applications (e.g. limited transport layer functions to support 2K block transfers for IEDs, RF and fiber support). DNP3 has been selected as a Recommended Practice by the IEEE C.2 Task Force; RTU to IED Communications Protocol.
DNP3 is an open and public protocol. In order to ensure interoperability, longevity and upgradeability of, protocol the DNP3 Users Group has taken ownership of the protocol and assumes responsibility for its evolution. The DNP3 Users Group Technical Committee evaluates suggested modifications or additions to the protocol and then amends the protocol description as directed by the Users Group members.
DNP3 Features:
DNP3 offers flexibility and functionality that go far beyond conventional communications protocols. Among its robust and flexible features DNP3 includes:
- Output options
- Secure configuration/file transfers
- Addressing for over 65,000 devices on a single link
- Time synchronization and time-stamped events
- Broadcast messages
- Data link and application layer confirmation
DNP3 was originally designed based on three layers of the OSI seven-layer model: application layer, data link layer and physical layer. The application layer is object-based with objects provided for most generic data formats. The data link layer provides for several methods of retrieving data such as polling for classes and object variations. The physical layer defines most commonly a simple RS-232 or RS-485 interface. DNP3 is very efficient for a layered protocol while ensuring high data integrity.
DNP3 Benefits:
Because DNP3 is based on the IEC 870-5 requirements, DNP3 is suitable for application in the entire SCADA environment. This includes RTU to IED communications, master to remote communications, and even peer-to-peer instances and network applications. It permits multiple masters and encourages distributed intelligence.
Users can expect many benefits from using DNP3. In the short term:
- Interoperability between multi-vendor devices
- Fewer protocols to support in the field
- Reduced software costs
- No protocol translators needed
- Shorter delivery schedules
- Less testing, maintenance and training
- Improved documentation
- Independent conformance testing
- Support by independent users group and third-party sources (e.g. test sets, source code)
Description of the DNP 3.0 Ethernet Driver
The Ethernet DNP 3.0 driver allows the FieldServer to transfer data to and from devices over Ethernet using DNP 3.0 protocol. The FieldServer can emulate either a Server of Client. The DNP 3.0 Ethernet Driver adheres to and supports the framework specified by the IEEE 1815-2012 Standard for electrical power system communications.
The following information was copied form the DNP 3.0 User Group Internet site.
The development of DNP3 was a comprehensive effort to achieve open, standardsbased Interoperability between substation computers, RTUs, IEDs (Intelligent Electronic Devices) and master stations (except inter-master station communications) for the electric utility industry. Also important was the time frame; the need for a solution to meet today's requirements. As ambitious an undertaking as this was, we reached this objective. And since the inception of DNP, the protocol has also become widely utilized in adjacent industries such as water / waste water, transportation and the oil and gas industry.
DNP3 is based on the standards of the International Electrotechnical Commission (IEC) Technical Committee 57, Working Group 03 who have been working on an OSI 3 layer "Enhanced Performance Architecture" (EPA) protocol standard for telecontrol applications. DNP3 has been designed to be as close to compliant as possible to the standards as they existed at time of development with the addition of functionality not identified in Europe but needed for current and future North American applications (e.g. limited transport layer functions to support 2K block transfers for IEDs, RF and fiber support). DNP3 has been selected as a Recommended Practice by the IEEE C.2 Task Force; RTU to IED Communications Protocol.
DNP3 is an open and public protocol. In order to ensure interoperability, longevity and upgradeability of, protocol the DNP3 Users Group has taken ownership of the protocol and assumes responsibility for its evolution. The DNP3 Users Group Technical Committee evaluates suggested modifications or additions to the protocol and then amends the protocol description as directed by the Users Group members.
DNP3 Features: DNP3 offers flexibility and functionality that go far beyond conventional communications protocols. Among its robust and flexible features DNP3 includes:
- Output options
- Secure configuration/file transfers
- Addressing for over 65,000 devices on a single link
- Time synchronization and time-stamped events
- Broadcast messages
- Data link and application layer confirmation
DNP3 was originally designed based on three layers of the OSI seven-layer model: application layer, data link layer and physical layer. The application layer is objectbased with objects provided for most generic data formats. The data link layer provides for several methods of retrieving data such as polling for classes and object variations. The physical layer defines most commonly a simple RS-232 or RS-485 interface.
DNP3 is very efficient for a layered protocol while ensuring high data integrity.
DNP3 Benefits: Because DNP3 is based on the IEC 870-5 requirements, DNP3 is suitable for application in the entire SCADA environment. This includes RTU to IED communications, master to remote communications, and even peer-to-peer instances and network applications.
Being an object-based application layer protocol, DNP3 has the flexibility to support multiple operating modes such as poll-response, polled report-by-exception, unsolicited responses and peer-to-peer. It permits multiple masters and encourages distributed intelligence.
Users can expect many benefits from using DNP3. In the short term:
- Interoperability between multi-vendor devices
- Fewer protocols to support in the field
- Reduced software costs
- No protocol translators needed
- Shorter delivery schedules
- Less testing, maintenance and training
- Improved documentation
- Independent conformance testing
- Support by independent users group and third-party sources (e.g. test sets, source code)
BACnet for Field Technicians (Free!)
Learning about BACnet? Want to update your BACnet knowledge? This free EBook will guide you through basic and advanced BACnet topics.
You can purchase a hardcopy of this book from Amazon or you can download the BACnet for Field Technicians for free from our website.
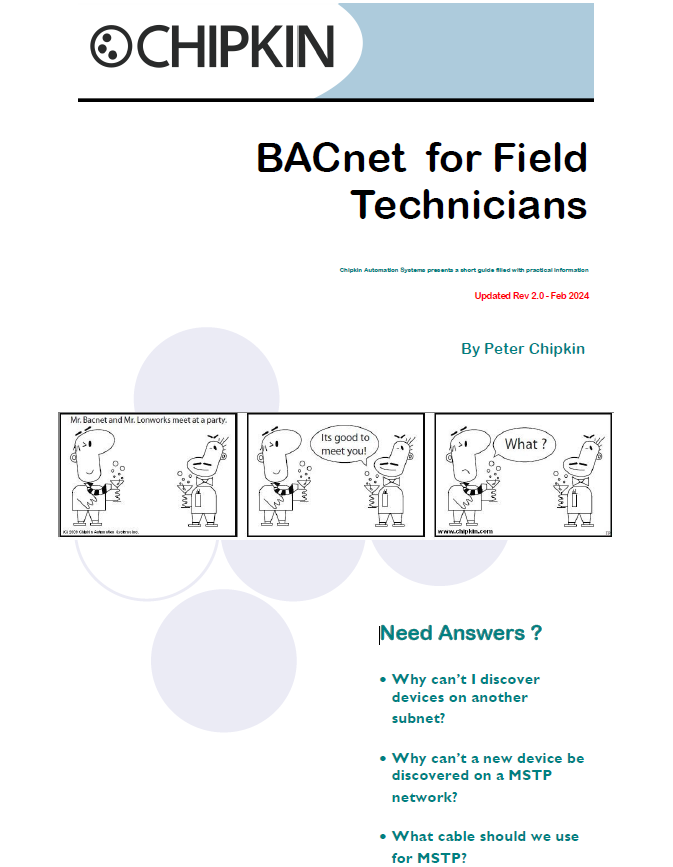
FREE CAS BACNET EXPLORER WITH THE PURCHASE OF A BACNET GATEWAY!
Purchase a FieldServer or CAS Gateway from us that contains any BACnet protocol and we will help you test and document the BACnet interface by providing a free full license to the CAS BACnet Explorer and a Hardcopy of the BACnet booklet.
The USB key and booklet ship with the product.
Thanks for choosing Chipkin's protocol gateways, data clients, and integration services to meet your building and industrial automation requirements!
Chipkin is a building and industrial automation protocol expert. We develop, configure, install and support gateways (protocol converters), data loggers and remote monitor and controlling applications. Founded in October 2000, Chipkin provides expert solutions for converting BACnet®, Modbus®, and LonWorks®—to name just a few—and enabling interfaces for HVAC, fire, siren, intercom, lighting, transportation and fuel systems. The high-quality products we offer (including those from other vendors) interface with Simplex, Notifier, McQuay, GE and many others—so you can rest assured that we will select the most appropriate solution for your application.
With Chipkin you are buying a solution. Our configuration expertise in this field combined with free BACnet and other tools ensure your success; and our customer support via phone, e-mail, and remote desktop tools means that we're there when you need us. Chipkin is a small responsive company, and we live or die by the quality of our service—and with offices in two-time zones—we can provide support when you need it. Give us a call now!
Customer Support
Chipkin is proud to provide support for the products we sell. For technical support, sales, and customer service, please contact us at 1 (866) 383-1657