Fully Automated 50-ton Bulldozer
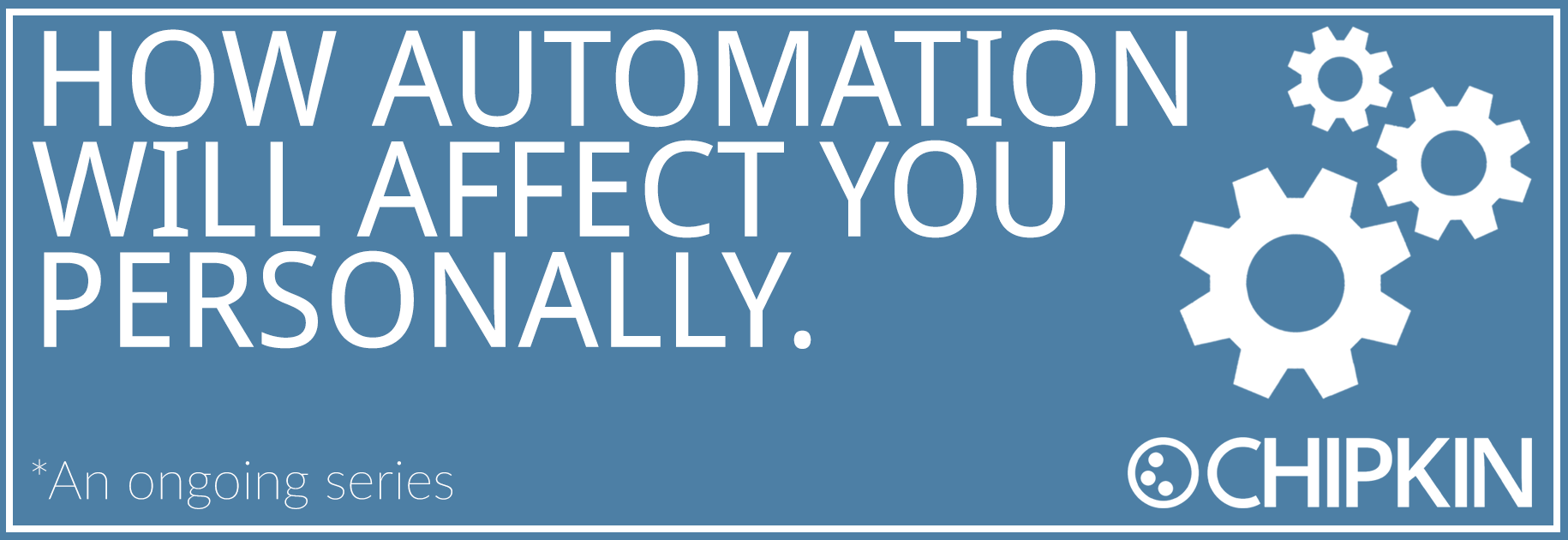
Intro to Automated Machinery:
With the advent of Autonomous driving technology, even large construction equipment like bulldozers, Excavators, Drilling machines are now driving fully autonomously! It's Incredible isn't it? Let's have a look at them.
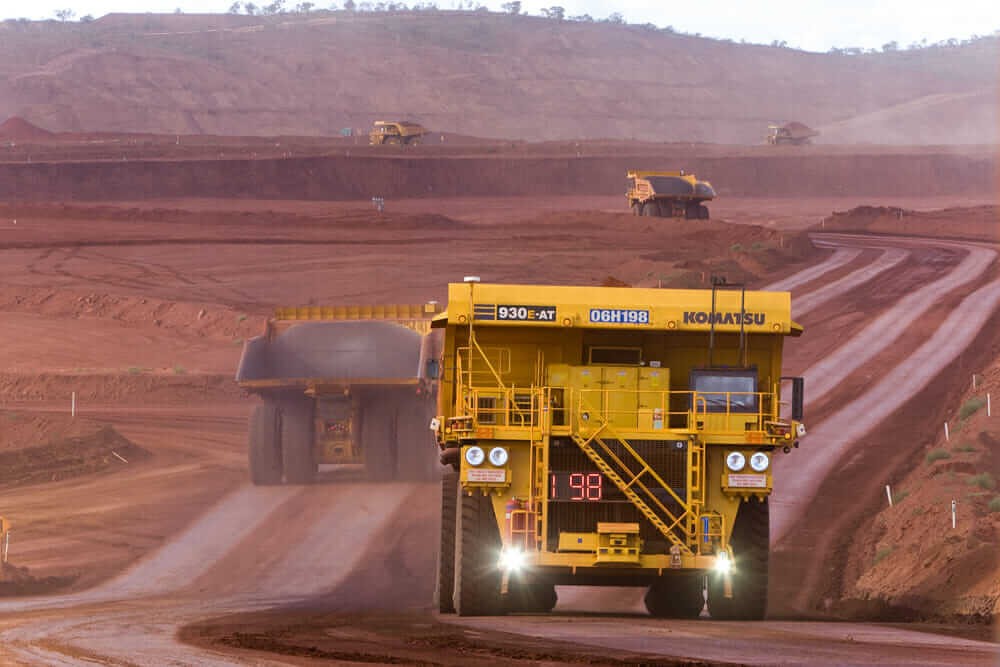
Fig: Autonomous dump trucks at Rio Tinto's Pilbara site.
At the nucleus of this robotic revolution are driver-less cars, which are now legal in 22 U.S. states and the District of Columbia and are expected to be available to the public as early as 2019 in the form of taxis and possibly 2021 for general purchase. But cars aren't the only vehicles ripe for automation.
Technology & Statistics:
- Much like the self-driving vehicles operated by companies like Waymo and GM, these robot bulldozers and back hoes use sensors like LIDAR and GPS to "see" the world around them. But unlike any of the autonomous cars driving around California or Arizona these days, these heavy movers use specially designed sensors to withstand the massive amounts of vibrations involved in excavation.
- Self-driving cars are programmed to be accurate down to the centimeter, but with autonomous construction equipment, operating within a confined, geofenced space without variables like pedestrians and bicyclists, the software that powers the machines can be much less precise.
- Heavy-equipment manufacturers are hard at work on autonomous construction vehicles that focus on making construction more efficient. In 2013, for example, Komatsu introduced the semiautonomous D61i-23 dozer, the world's first dozer with fully automatic blade control. Caterpillar and John Deere are working on similar vehicles, which likewise will be semi-autonomous to start with, but ultimately will evolve toward full, driverless automation. And in the San Francisco Bay Area, Built Robotics has automated excavators already on job sites (though the vehicles still require human supervision).
- Fatal injuries among construction and extraction occupations rose by 2 percent to 924 cases in 2015, according to the US Bureau of Labor Statistics — the highest level since 2008. Meanwhile, 70 percent of construction firms lack skilled workers, potentially stalling commercial and home building projects.
Fig: HX2 autonomous carrier
Remote Control Systems
Operator-assist technologies control specific machine functions to boost productivity and cut costs. Remote control systems that move operators out of cabs and away from hazards. And in some cases, fully autonomous trucks. Massive haulers. Two stories tall. Carrying 250-ton payloads. With no operators in sight. With multiple levels of remote control and even semi-autonomous operation, Cat® Command for dozing helps you increase operator safety and comfort — and increase the productivity of your dozer fleet.
Whether you choose the over-the-shoulder remote control console or the remote operator station, your operators can have full control of the dozer without exposing themselves to dust, noise, vibration or any of the other hazards a dozer experience. And with semi-autonomous dozing, a single operator can automate the push process for up to three dozers, dramatically increasing your fleet's productivity.
Fig: Located in a trailer about 300 feet away, an operator is remotely controlling a Caterpillar D11T dozer.
Advantages of autonomous construction equipment
- Increased safety
- Increased productivity
- Ease of operations
- Increased efficiency
- Cost cutting
Safety Features
The self-driving excavators have three layers of redundant safety features.
- The first is object detection, including obstacle avoidance using lidar, so that the machines avoid hitting people or other vehicles.
- The second is a geofence that defines the exact perimeter where the equipment can operate.
- The third layer is a good old-fashioned kill switch; One that is mounted on the machine and another that is wireless
How do these huge vehicles work autonomously?
- First, the vehicle needs to know where it is and its orientation. The primary location system used is Global Navigation Satellite System (GNSS) -based and is often mounted around the cab. There are a variety of GNSS systems deployed and operational. In North America, the one we are most familiar is GPS. However, regular GPS is only accurate to about 6-10 meters, which is not adequate for this application; regular GPS cannot provide heading information unless the vehicle is in motion. These limitations are addressed using either Differential GPS (DGPS) or Real Time Kinematic (RTK) GPS, both require a local stationary GPS receiver for which its location is precisely known. The stationary receiver compares its known location to its location as calculated by the GPS receiver. From this information it can generate corrections which it transmits to the other mobile GPS receivers located on the vehicle.
- To supplement GPS and RTK, an Inertial Measurement Unit (IMU) is installed in the vehicle usually centrally located to the vehicle. The heading limitation of GPS is overcome by using two GPS receivers (1- Dual GPS Antennae) on the excavator with the antennas separated in space by some reasonable distance (1 to 2 m). The absolute position of receiver 1 to receiver 2 antennae is used to calculate the absolute heading.
- System Architecture:
Fig: Sensor positions in an excavator
- The stationary GPS transmits the GPS correction to the RTK system on the vehicle via a 3G/4G or radio link. The vehicle RTK system uses the information to correct its position calculations. The main CPU then calculates the position of the bucket using the corrected RTK position, chassis IMU (often embedded in the RTK system), boom, stick, and bucket sensors, along with the known geometry of the excavator.
- It compares the site survey and the site plan loaded into its memory. It can now control the movement of the vehicle and the excavation process through the hydraulic control to remove the material in the site survey which is not in the site plan.
Fig: Autonomous CAN System Architecture